Explore the world of Industry 4.0 in this comprehensive guide. Understand its key components, benefits, challenges, and impact on the future of manufacturing. Dive into the era of smart factories, IoT, AI, and more as we unravel the Fourth Industrial Revolution.
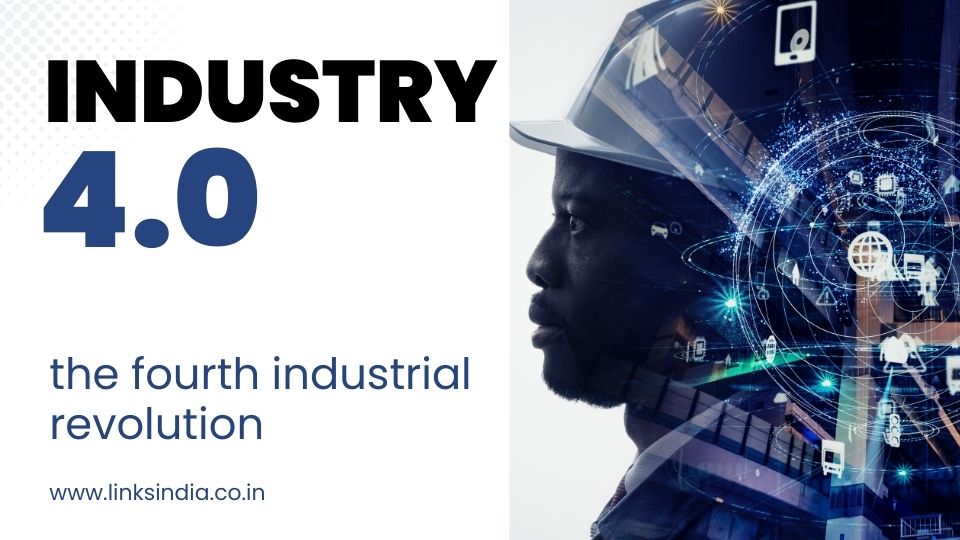
Unraveling Industry 4.0: The Dawn of a New Industrial Revolution
Introduction
Welcome to the era of Industry 4.0, the fourth industrial revolution that is reshaping the manufacturing landscape by integrating automation, data exchange, and innovative technologies. This revolution is not just about industrial automation; it’s about the fusion of the physical and digital worlds. This blog post will delve into the depths of Industry 4.0, exploring its key components, benefits, and potential challenges.
Understanding Industry 4.0
Industry 4.0, also known as the Fourth Industrial Revolution, is a term that encapsulates the current trend of automation and data exchange in manufacturing technologies. This includes cyber-physical systems, the Internet of Things (IoT), cloud computing, and cognitive computing.
The Concept of Smart Factory
At the heart of Industry 4.0 is the concept of the “smart factory”. These factories are characterized by their ability to adapt and learn from data, making them more efficient and effective. Cyber-physical systems within these factories monitor physical processes and make decentralized decisions, communicating and cooperating with each other and humans in real-time.
The Evolution of Industry 4.0
The journey to Industry 4.0 has been a gradual evolution. The first industrial revolution was characterized by mechanization with water and steam power. The second brought mass production with the help of electricity, while the third introduced computers and automation. Today, the fourth industrial revolution builds on the digital revolution, blurring the lines between physical, digital, and biological spheres.
Key Components of Industry 4.0
Industry 4.0 is not a single technology but a suite of technologies. Let’s delve into the key components that make up this revolution.
Internet of Things (IoT)
IoT is the network of physical devices, vehicles, and other items embedded with sensors, software, and network connectivity that enables these objects to collect and exchange data. In the context of Industry 4.0, IoT devices can monitor and optimize production processes, improving efficiency and reducing waste.
Industrial Internet of Things (IIoT)
A subset of IoT, the Industrial Internet of Things (IIoT), refers to interconnected sensors, instruments, and other devices networked together with computers’ industrial applications, including manufacturing and energy management. This connectivity allows for data collection, exchange, and analysis, potentially facilitating improvements in productivity and efficiency as well as other economic benefits.
Cyber-Physical Systems (CPS)
CPS are integrations of computation, networking, and physical processes. Embedded computers and networks monitor and control the physical processes, with feedback loops where physical processes affect computations and vice versa. In Industry 4.0, CPS plays a crucial role in monitoring physical factory processes and making decentralized decisions.
Cloud Computing
Cloud computing involves delivering different services through the Internet, including data storage, servers, databases, networking, and software. In Industry 4.0, cloud computing allows manufacturers toquickly scale up or down their operations, provides flexibility, and reduces the cost of hardware.
Cognitive Computing/AI
Cognitive computing and AI involve machines learning from experience, making human-like decisions, and carrying out tasks that would normally require human intelligence. In the context of Industry 4.0, AI can be used to analyze data to uncover insights, predict outcomes, and even make decisions.
Autonomous Robots
Autonomous robots are capable of performing tasks with a high degree of autonomy. In Industry 4.0, these robots work alongside humans, learning from their actions, and improving over time. They can perform a variety of tasks, from picking and packing to more complex tasks like assembly and inspection.
Additive Manufacturing
Additive manufacturing, also known as 3D printing, involves creating three-dimensional objects from a digital file. This technology allows manufacturers to produce small batches of customized products on demand, reducing waste and inventory costs.
Big Data Analytics
Big data analytics involves examining large and varied data sets to uncover hidden patterns, unknown correlations, market trends, customer preferences, and other useful information. In Industry 4.0, big data analytics can provide valuable insights for business decision-making, improving efficiency, and driving innovation.
Benefits of Industry 4.0
Industry 4.0 offers a multitude of benefits that can drive growth, efficiency, and competitiveness.
Increased Efficiency
By automating routine tasks, companies can increase efficiency and productivity. Machines can work around the clock and are often faster and make fewer mistakes than humans.
Improved Quality
With advanced technologies like AI and machine learning, companies can improve the quality of their products. These technologies can detect and correct errors in real-time, reducing the cost of defects and rework.
Enhanced Decision Making
With access to real-time data and analytics, companies can make more informed decisions. This can lead to better resource allocation, improved process optimization, and increased profitability.
Customized Production
Industry 4.0 technologies enable more flexible and customized production. Companies can produce small batches of customized products at a lower cost, meeting the increasing demand for personalized products.
Challenges and Solutions
While Industry 4.0 offers significant benefits, it also presents challenges that need to be addressed.
Data Security
With the increased connectivity and use of cloud services, data security becomes a significant concern. Companies need to implement robust security measures to protect sensitive data.
Lack of Skilled Workers
The shift to a digital industrial economy requires a workforce with strong technical skills. There is a need for continuous training and education to equip workers with the necessary skills.
High Initial Investment
Implementing Industry 4.0 technologies can require a significant initial investment. However, the long-term benefits such as increased efficiency and productivity can offset these costs.
FAQs
- What is Industry 4.0? Industry 4.0, also known as the Fourth Industrial Revolution, is a term that describes the current trend of automation and data exchange in manufacturing technologies. This includes cyber-physical systems, the Internet of Things (IoT), cloud computing, and cognitive computing.
- What are the key components of Industry 4.0? The key components of Industry 4.0 include Internet of Things (IoT), Cyber-Physical Systems (CPS), Cloud Computing, Cognitive Computing/AI, Autonomous Robots, Additive Manufacturing(3D Printing), and Big Data Analytics.
- What are the benefits of Industry 4.0? The benefits of Industry 4.0 include increased efficiency, improved product quality, enhanced decision-making, and the ability to produce customized products.
- What are the challenges of Industry 4.0? Some of the challenges of Industry 4.0 include data security issues, a lack of skilled workers, and the high initial investment required to implement Industry 4.0 technologies.
- How does Industry 4.0 affect the workforce? Industry 4.0 is likely to lead to a shift in the types of jobs available, with a greater need for workers with strong technical skills. However, it can also lead to job displacement due to automation. It’s important for companies and governments to provide training and education programs to prepare the workforce for these changes.
Conclusion
Industry 4.0 marks a new era in the industrial sector, characterized by smart factories and advanced technologies. While it presents several challenges, the potential benefits it offers in terms of efficiency, quality, and decision-making are immense. As we continue to navigate this digital industrial revolution, continuous learning, adaptation, and innovation will be key to staying competitive. As the saying goes, the only constant is change, and Industry 4.0 is a testament to that.